CC-Link IEF Basic iQ-R and iQ-F with robot FR series (CR800 controller)
This is a shortened version of Ethernet Function manual and it covers only IEF Basic communication setup between iQ-R and iQ-F PLC and one MELFA robot as a slave.
iQ-F settings describe in attachment.

"Copyright © Mitsubishi Electric Europe B.V.
IMPORTANT !
These Function Blocks are demo versions that are only intended to demonstrate program functions and provide general orientation for your software choices. They are not suitable for use in real applications! "
"Improper use of demo versions in applications can lead to serious malfunctions and damage! Programs for real applications must always be configured for the individual application by trained staff and tested thoroughly before being used.
Mitsubishi Electric cannot assume any liability if these examples are used in real applications."
Robot parameter settings
In RT Toolbox 3 set up Ethernet parameters in Online -->Parameter-->Communication Parameter -->Ethernet
Remember, that engineering station, PLC and the robot have to be in the same subnetwork
Picture 1. Check your communication settingsIn RT Toolbox3 enable CC Link IEF Basic function in Online -->Parameter Field Network Parameter -->CC Link IE Field Basic
Picture 2. Enable CC Link IE Field BasicWrite the changes to the robot controller and restart it.
PLC parameter settings
In GX Works3 enable CC-Link IEF Basic function in Parameter -->RxxCPU --> Module Parameter Own Node Settings. In order to do this, change 'To use or Not to Use CC Link IEF Basic Setting' to Enable.
Picture 3. Enable communication in PLCOpen Network Configuration Settings
Select Detect Now --> Yes --> OK
Picture 4. Detect all devices in the networkRight-click on found module and change module to CC Link IEF Basic
Press Close with reflecting the setting --> Yes
Go to Refresh Settings and assign slave devices to PLC Devices.
Picture 5. Sample Refresh SettingsExemplary settings are shown in the picture above:
- RX0-RX63 Dec (RX0-RX3F Hex) is assigned to B0-B63 Dec (B0-B3F Hex)
- RY0-RY63 Dec (RY0-RY3F Hex) is assigned to B4096-B4159 Dec (B1000-B103F Hex)
- RWr0-RWr31 Dec (Rwr0-Rwr1F Hex) is assigned to W0-W31 Dec (W0-W1F Hex)
- RWw0-RWw31 Dec (RWw0-RWw1F Hex) is assigned to W4096-W4127 Dec (W1000-W101F Hex)
Apply the changes, go to Online and write them to PLC.
Diagnostics and application
In Diagnostics dropdown menu select CC Link IE Field Basic Diagnostics and check the connection.
Picture 6. Communication 'Diagnostics' windowCopy the programs attached to this guide and paste them to the respective devices. These programs are created to test the communication between the Robot and the PLC.
On the robot side, the program sets outputs of the robot to 1 with M_Out, then it sends words to CC-Link outputs with M_Dout
On the PLC side, the program reads these values and moves them to its own outputs – bits to bit outputs, words to word outputs.
Results of these programs cooperating are shown on the pictures below.
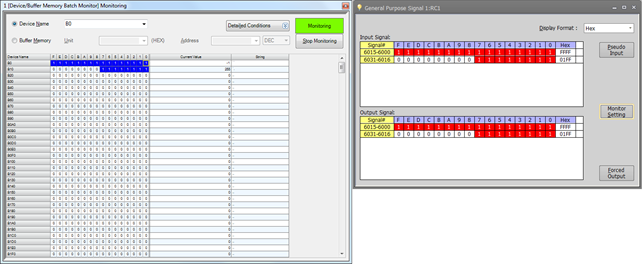

Attachments:
File name: | Description: |
| |
IEF Basic PLC.txt | IEF Basic communication program example for the PLC side. Copy the contents of the file into the project. |
| |
IEFBASIC.prg | IEF Basic communication program example for the MELFA Robot side. Copy this program into the project. |