PLC configuration
Creating new project
Startup GX Works3 and create new project. Select the model of the PLC CPU being used and a program language to be used in the PLC CPU on the window below. After completing the selection click the OK button.
Module configuration
Open Module Configuration from the project tree. Create configuration of your PLC by dragging and dropping modules form Element Selection window.

To use Motion Module in Simple Motion mode you have to place module with ending (S). Only 4, 8 or 16 axis module can be use in Simple Motion mode.
Network configuration.
To create network configuration go to Module Parameters (Network) >> Network Configuration Settings >> Detailed Setting.
In CC-Link IE TSN Configuration window create configuration by adding devices from Module List to the network configuration. Each device is identified by the IP Address. Network part (first three octets) of IP address is determined by the IP Address of master module, last octet needs to be set by switches on slave module (amplifiers and remote IOs). In column Motion Control Station check stations (servo axes) that will be used as a Axes in Simple Motion. The rest of devices will be used as standard network device. It is necessary to assign them RX, RY, RWr and RWw base on specification of those devices.
When configuration is ready close this window with saving the settings.
Axes definition
It's necessary to define axes in Simple Motion module and assign servo drives as a network devices to the appropriate axis. To define axes go to Simple Motion Module Settings of RD78G module. In Simple Motion Module Setting Function assign IP Addresses of the servo amplifiers to the axes in parametr Pr.141.
When configuration described above is finished convert project in GX Works3 and download it to PLC.

When writing project to the PLC for the first time download only PLC Parameter (without RD78G parameters), make PLC restart and then download to the PLC parameters of RD78G module. PLC needs this sequence to switch module from PLCopen Mode to Simple Motion Mode.
After restarting whole system communication with all devices should startup. It can be confirmed by D LINK LED on modules and r01, r02,.. on servo amplifiers.
Servo parameter setting
To set parameters of servo drives we need to use MR Configurator2. It can be used as independent software or through GX Works3. In first case single axis connection through USB cable and multi-axis connection through the network is possible. Using MR Configurator2 as a separate software allows to set parameters directly in servo amplifiers, use all monitoring and diagnostic functions. Project is saved as a separate file.
in second option, when MR Configurator2 is used through GX Works3, it is possible just to set servo parameters. It's not possible to use monitoring and diagnostic functions, but in this case all servo parameters are stored in GX Works3 project. It is also possible to force PLC to automatically write servo parameters to the drives during system startup.
Setting parameters through GX Works3
Go to the Module parameters (Network) of RD78G module and open Network Configuration Setting. In CC-Link IE TSN Configuration window go to Parameter Automatic Setting column and double click Detail Setting for one of axes. MR Configurator2 will open. Settings done in MR Configurator2 can be written to the amplifiers directly or you can close MR Configurator2 with saving settings, then check tick in Parameter Automatic Setting column. It will cause that servo parameters will be written to the amplifier automatically during system startup.
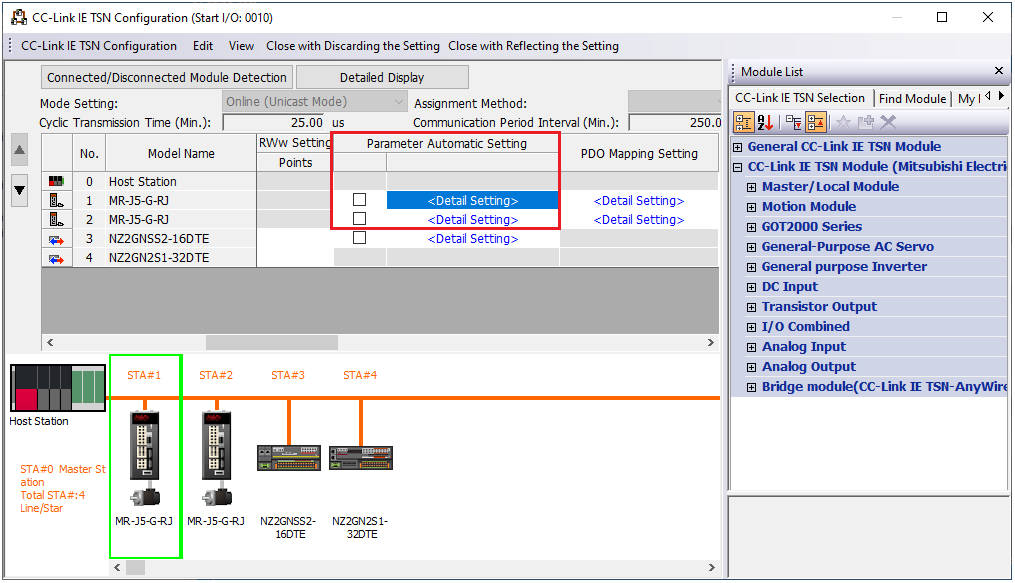
Setting parameter directly through MR Configurator2
Open MR Configurator2 and create new project. Switch to Multi-axis project and define connection with amplifiers. It is possible to communicate directly with amplifiers through CC-Link IE TSN or communicate through PLC using USB or Ethernet connection.
Required parameter setting
During startup of the system with RD78G module in Simple Motion mode module forces values in part of the amplifier parameters like electronic gear, Sensor input method,... Those parameters can't be modified, otherwise it will cause module error. Despite of parameters forced by module you may need to set few additional parameters required by application like Forced stop disable, Absolute positioning mode, homing method and parameters,...
Programming
The RD78G module in Simple Motion mode can be programmed as standard Simple Motion module that base on SSCNET III/H or CC-Link IE Field. It is possible to use built in module labels, built in function blocks or PLCopen libraries.

You may find lot of articles describing programming of the Simple Motion modules
Differences between RD78G in Simple Motion mode and RD77MS module
Homing
In system based on CC-Link IE TSN homing is executed by servo drive. Method and parameters regarding homing needs to be set in servo parameter not in simple motion module parameter. Starting of the homing looks exactly the same like in standard simple motion module.

For more information refer to the article:
Mark detection
Because module doesn't have inputs onboard it uses inputs of the amplifier as a mark detection input. It can be input TPR1 of servo amplifier or DOG input. In case of DOG input sampling time is limited to one scan of the module. In case of TPR1 sampling time is equal 1us. From programming point of view function works almost the same like in Simple Motion module.

For more information refer to the article:
Synchronous encoder
RD78G module doesn't have encoder input to connect external encoder. Encoder via servo amplifier have to be use.

For more information refer to the article: