This article describes functionality of Motorizer - servo selection tool
Motorizer introduction
Motorizer is a free software designated for selecting proper servomotor to the application. It includes most common types of load mechanisms like:
- Ball screw
- Rack and pinion
- Roll feed
- Rotary table
- Elevator
- Conveyor
- Crank
- Linear servo
- Generic rotary
For downloading Motorizer please visit one of these pages:
LINK
Motorizer training materials
Webinars
Polish customers had opportunity to take part in an on-line training during series of webinars held by Mitsubishi. Video from the training may be found under link below.
Presentations
You can find full Motorizer training presenation in attachments of this article.
Navigation in program
After clicking list icon in upper-left corner of the application the main menu should expand. In this section you can perform following things:
- New project (single axis) - creating new single axis project
- New project (multi-axis) - creating new multi-axis project. This option is usefull for selecting configuration for the whole machine. Motors can be divided into gropus with common DC bus or completely seperate drives.
- Open - opening existing project
- Save - saving current project
- Save as - saving current project under different name
- Print - printing selection report
- Motor specifications - motor datasheets
- Setting - main settings of the application like: units, language, layout
Filter setting
Filter setting section is divided into "Motor selection" filters and "Drive selection" filters. It is used for filtering the result of the selection after filling all of specification settings.
Filter setting - Motor selection
Motor selection most usefull filters includes:
- Motor selection candidate - check motor series you're interested in or leave this setting for automatic selection
- Motor display - you can choose if you would like to see in the results: servo motors / inverter(asynchronous motors) / sensorless servo
- Power supply voltage(common for motor and drive selection): 24V DC / 48V DC / 100V AC / 200V AC / 400V AC
- Capacity - Unspecified(only best results will be shown) / kW(filter depending on power of motor) / Nm (filter depending on nominal torque of motor) / A (filter depending on nominal current of motor)
- IP rating
- Brake - set if motor should be equipped with brake
- Oil seal - set if motor should have additional oil seal
Don't use Transmission mechanism section as it is dedicated for series of servo motors integrated with hypoid gearboxes available only in Asia.
Screen of this section is presented below.
Filter setting - Drive selection
Drive selection most usefull filters includes:
- Drive selection candidate - check drive series you're interested in or leave this setting for automatic selection
- Motor display - you can choose if you would like to see in the results: servo motors / inverter(asynchronous motors) / sensorless servo
- Power supply voltage(common for motor and drive selection): 24V DC / 48V DC / 100V AC / 200V AC / 400V AC
- Capacity - Unspecified(only best results will be shown) / kW(filter depending on power of motor) / A (filter depending on nominal current of motor)
- Regenerative option - set if breaking resistor will be needed or leave it set as unspecified for automatic selection
- Command interface - set communication type
Selection candidate list
After fiiling all 3 steps with required data in selection candidate list you'll see some suggestions of the motors applicable for the application.
In subsequent columns we can find information such as:
- Checkbox - selection of the motor. Selected motor will stay on the list even if it won't fullfill all of required parameters.
- Drawing pin - you can mark the motor with the pin so it won't be deleted from the list after not fullfiling all of required parameters.
- Motor β name of the servomotor,
- Motor capacity[kW] β capacity of the motor,
- Drive β model of servoamplifier suitable for selected serwomotor,
- Effective torque β RMS value of torque [Nm],
- Torque effective load rate - π_π
ππ/π_π
ππ‘ππ β100%,
- Peak torque β maximum value of torque,
- Peak load rate - π_πππ₯/π_π
ππ‘ππ β100%, should be lower than 300%,
- Effective torque at stop β value of torque while motor is at stop,
- Effective load rate at stop - π_π π‘ππ/π_π
ππ‘ππ β100%, should be lower than 70%,
- Motor output - RMS value of motor power [W],
- Motor output rate β P_RMS/P_Rated β100%,
- Maximum speed β maxium speed of motor,
- Maximum speed rate - v_max/v_Rated β100%,
- Maximum load inertia moment β maximum intertia moment of load,
- Inertia moment ratio - I_load/I_motor - maximum ratio is different for every motor,
- Regenerative power β power generated during braking,
- Regenerative load rate - P_braking/P_(max-braking) β100%,
- Regenerative option β needed if there is power generated during braking
- Rated speed β rated speed of motor
- Torque effective load rate β RMS of torque should be lower than 100%.
- Peak load rate β for a short time, the peak load can increase up to 300%.
- Effective load rate at stop β only for motors in Z-axis. According to documentation it should be maxium 70% but in some cases 80% is also acceptable.
- Motor output rate β it should be lower than 100%.
- Maximum speed rate β it should be lower than 100%. If it is too high try changing gearbox for a model with lower ratio.
- Inertia moment ratio β too high inertia moment ratio can cause overshoot of position. Every motor has itβs own recommended inertia moment ratio.
- Regenerative load rate β when big masses are moved there may be necessity of using some additional regenerative resistors. Motorizer should propose some solutions if needed.
There are 3 types of results:

motor selection is correct

motor selection needs revising, one of the parameters is close to critical value

motor selection is incorrect, one of the parametres exceeded critical value
Selection examples
Whole selection process is divided into 3 steps:
- Definition of load mechanism and it's parameters like mass of load, dimensions of the mechanical parts, inertia of elements and forces.
- Definiton of transmission mechanism elements like couplings, gearboxes, toothed belts etc.
- Definition of operation pattern.
Ball screw
Description of application:
15 kg
trolley is mounted
horizontally on a ball screw
. The screw itself has a lead
of 20mm
and a
diameter of 20mm
. Select the drive so that the truck travels
0.1 m
in one direction and returns back to the starting position. He will stand in each position for
500m
s. The whole cycle time is
3s
. This movement profile will always be the same throughout the life of the machine. Skip friction, weight on the trolley and moments of inertia of elements not described above.
Load mechanism definition:
If you don't know approximate value of load inertia then calulcate it using "calculator" implemented in the software.
Operation pattern definition:
After filling all required data you'll see the list of motors suitable for application. Choose the motor depending on it's series(low inertia / ultra low inertia), power and required safety factor.
Conveyor - belt driven unit
Description of application:
On a 35cm wide conveyor, inclined at an angle of 15 degrees to the horizontal, details are transferred in indexing mode. Details move by 50mm in 0.2s, with 1s intervals.
The roller driving the conveyor has a diameter of 65mm.
The belt of the feeder weighs 8kg.
Workpiece weight 200g, at the same time on the feeder can be up to 35 details.
Load mechanism definition:
Operation pattern definition:
Transmission mechanism definition:
The best way to select proper gearbox is to wait for selection until fullfiling steps 1 and 3. After that you should see first suggestions of proper servo motors. Check parameters below:
- Torque effective load rate - if torque is too big choose bigger ratio.
- Maximum speed - bigger gearbox ratio means bigger motor speed. Please try not to exceed nominal speed of the motor because torque characteristic drops then.
- Maximum load inertia moment - load inertia is reduced in square by gearbox ratio. If this parameter is too high try choosing bigger ratio.
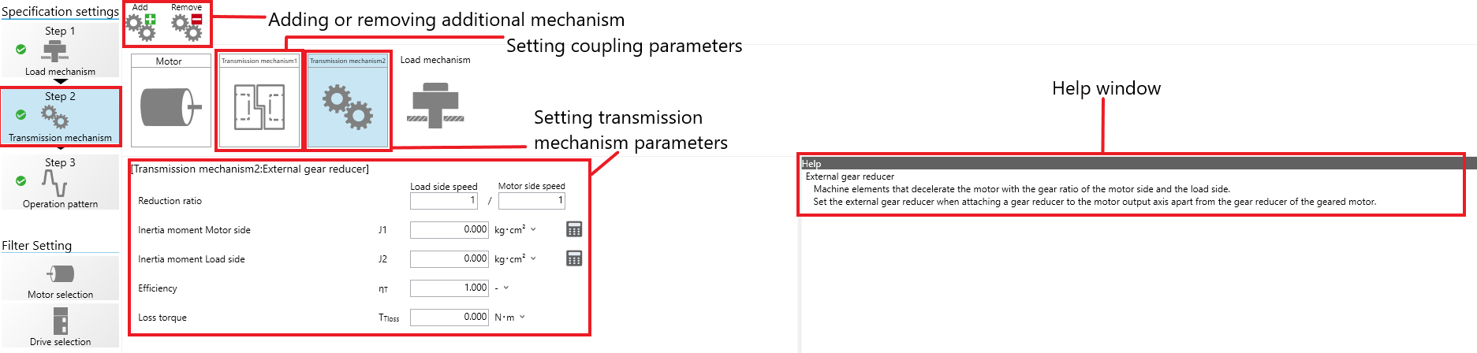